sheet metal drawing operation is used to make
Its used to make parts for many industrial fields. If the strength allows the method of grooving first and then bending is preferred to make small sheet metal bending radius.
The sheet feeds into a press that punches out round pieces that will be formed into counts.
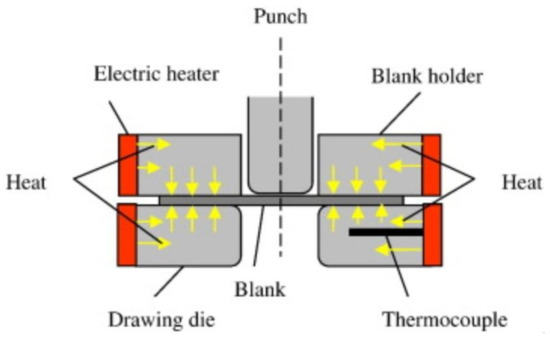
. Extremely thin sheets are considered foil or leaf and pieces thicker than 6 mm. As per drawing - It should have one adjustable shelf for effective space utilization - Doors per unit shall be as per drawing - All edges shall be provided with machine pressed 2mm thick PVC lipping edge binding 4. Its an alloy of copper containing both tin and phosphorusThis gives the metal more fluidity in its molten state allowing for easier casting and molding processes like press punching bending and drawing.
When it comes to choosing the best custom rubber stamp for your needs the first thing you should consider is the difference between self-inking and. Yield strength is uniform and there is no clear direction. In this process the workpiece sheet metal placed over the die and a punch exerted the force on the workpiece by this force sheet metal extend and filled the cavity and takes the shape of the die.
Related
This is done through the application of force on a workpiece. The lines required for marking are drawn by the scriber. Bending of sheet metal is a common and vital process in manufacturing industry.
So it is very important to design an economy friendly and time-saving press tools. The sheet metal bending can be properly smaller and can not be operated less than the ratio of plate thickness to groove width of 14. Bending is one of the most common sheet metal fabrication operations.
It is the most common type among various press brakes also been called sheet metal brake. Steps to design any Sheet metal stamping press tool or die. Sheet metal bending is the plastic deformation of the work over an axis creating a change in the parts geometry.
The punch press actually performs two operations it punches out a disc 14 centimeters in diameter then bends it into a cup. For making any type of operation on a sheet you need to mark on the sheet as per the requirement of the final job piece. The sheet is drawn into the die hole taking the shape of the cavity.
But what if press tool is not working efficiently or it takes many more operations to produce stamped parts. The punch often passes through the work into a dieA scrap slug from the hole is. Many sheet metal stamping types are available and they are chosen based on the shape and the size.
Similar to other metal forming processes bending changes the shape of the work piece while the volume of material will remain the same. The die is clamped using the blank-holder. The sheet metal stamping process is a very fast and precise manufacturing process.
Sheet metal is metal formed by an industrial process into thin flat pieces. In Sheet Metal working industry a wide range of power and hand operated machines are used. The project employee by using the roller for bending purpose by manual.
A blank-holder is used to clamp the blank on the die while the punch pushes into the sheet metal. Also known as press braking flanging die bending folding and edging this method is used to deform a material to an angular shape. This machine can be used in various fields.
Manual press brakes are required to adjust the bending dimensions and angles manually. Our project the sheet metal rolling is very simple in operation by using roller which is coupled with handle. Punching is a forming process that uses a punch press to force a tool called a punch through the workpiece to create a hole via shearingPunching is applicable to a wide variety of materials that come in sheet form including sheet metal paper vulcanized fibre and some forms of plastic sheet.
Cracks occur during bending deep drawing and molding which is wasted. The force must exceed the materials yield strength to achieve a plastic deformation. The sheet is about a meter and a half wide and a roll like this is long enough to make three-quarters of a million drink counts.
Sheet metal is one of the fundamental forms used in metalworking and it can be cut and bent into a variety of shapesCountless everyday objects are fabricated from sheet metal. Thicknesses can vary significantly. When you require to produce an arc or a circle on the sheet the divider is used for drawing the arc or circle.
In this operation forming of a flat metal sheet into a hollow or concave shape like a cup is performed by stretching the metal in some regions. Deep or cup drawing. In this operation a hollow cup shape die is used.
Hand Tools used in Sheet Metal. - Planter box shall be of 19mm thick Ply board with GI sheet at base of planter vase. Simple operation low labor intensity easy to realize mechanization and automation and high productivity.
Phosphor bronze is known for high performance processability and reliability. Browse through our extensive lineup of different models and find a stamp that will help make your life easier by automating repetitive writing from signatures to dates to whatever else you need. From another point of view the press brake can be divided into.
Sheet Metal Forming An Overview Sciencedirect Topics
Sheet Metal Forming Processes And Equipment Machinemfg
Deep Drawing Find Suppliers Processes Material
Sheet Metal Forming Processes Total Materia Article
Deep Drawing An Overview Sciencedirect Topics
Sheet Metal Forming Basics Processes And Material Used
9 Different Types Of Sheet Metal Operations With Diagram Pdf
Deep Drawing Metallurgy For Dummies
Tube Manufacturing Tube Drawing And Tube Extrusion
Deep Drawing Operation In Sheet Metal Smlease Design
Deep Drawing An Overview Sciencedirect Topics
Deep Drawing An Overview Sciencedirect Topics
Deep Drawing Operation In Sheet Metal Smlease Design
Metals Free Full Text Recent Developments And Trends In Sheet Metal Forming Html
Custom Deep Drawn Parts Capabilities Trans Matic Metal Stamping Process Metal Forming Metal Stamping